AFTER SALES SERVICES
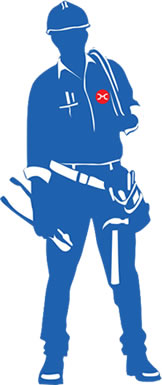
CMC Industries portfolio includes also a variety of after sales services foreseen to maximize both performances and operational reliability of installed products and system.
A wide range of training opportunities are available, either in our training center at CMC Industries headquarter or directly at Customer's site, for qualifying Customer's personnel to be perfectly prepared for everything that could be required during the operative life.
Preventive and corrective maintenance services are also available as both remote service and on-site assistance, this to allow at all times the best possible performance and availability.
Spare parts service is available to support any need of consumable or wear parts, as well as of possible replacement. This service could be arranged with a combination of a minimum set of parts stored locally and a wide range of parts stored in our warehouse that can be shipped almost immediately through Couriers everywhere in the world.
Operative lifetime can be extended over the initially estimated period by customized modernization activities that will bring the system / product to a new life.
Modernization is not intended as a simple replacement of worn or obsolete parts with new component, it could arrive to include a complete redesign in order to fit with new operative requirements or to increase energy efficiency / reduce operative costs.
Training and qualification
CMC Industries training are customized on Customers' needs and vary in a wide range of contents and formats from basic to advanced trainings and depending from factors like the skill of attendants or the topics to be discussed (i.e. use of a machine, maintenance of a system, and so on).
Common characteristic of all trainings is the aim to offer to Customers' personnel the opportunity for fully conducting their products / systems while minimizing costs and any residual risk.
Benefit of training performed in our training center at CMC Industries headquarter is the possibility to have access to the workshop area, becoming so familiar with the different realization phases, and to be far away from time pressure and disruptions of live operations. Benefit of training performed at Customer's site is the possibility to work directly on the real system analyzing in a deeper way all site specific topics. This of course need a preliminary planning from the Customer as it could interfere with operative activities.
CMC Industries suggest, to get benefit of both solutions while minimizing the impact on operations, to combine the solution with a "training on the job" where maintenance Personnel works beside our Personnel during execution of site activities, and a dedicated training at our training center.
During the training, with the purpose of increasing the knowledge of all potential areas of failure and among all other topics, our experienced trainers will provide a broad overview of all working procedures with particular focus to Safety, normal operations and maintenance, inspection and troubleshooting, handling of documentation (drawings, manuals, spare part lists).
Attendants to the training, upon its completion, receives a certificate that states their capability to conduct maintenance and repair works.
Remote service and on-site assistance, hotline support
CMC Industries Customer Service Team is always available to put its experience at support of Customer needs, whenever and whatever would be needed, everywhere in the world.
Our Team is prepared to work hard for keeping your system in operation with the best possible performance at all times. Particularly referring to the business of Poultry division, this means 24/7.
Remote services could vary from the hotline support, where our engineers interact with Customer personnel offering their expertise for advising and to identify and fix any issue, up to the execution of activities directly on site.
Different packages of "on site assistance" could be defined in order to fit in the best possible way with Customers' needs; this from the experienced specialist that support the Customers' maintenance team, through the availability of a supervisor that support the daily operations while providing for repairs, up to the availability of a resident engineer that is fully integrated with the local team for performing maintenance activities at all levels.
In case you would be interested in more details concerning our remote support / hotline service, or whether you would require onsite assistance or spare parts, you are kindly asked to contact us at indicated phone / e-mail addresses or to fill the contact form here below.
Preventive and corrective Maintenance
Maintenance refers to the whole package of actions (technical, administrative and supervision) to keep a system in operation or to bring it to a condition compatible with the execution of expected functionalities. The activities, depending from the triggering event, can be divided in two main categories:
Corrective (or reactive) maintenance refers to those activities performed upon request to rectify a failure bringing the system again in operation and properly performing the expected functionalities. This category includes also the extraordinary maintenance, intended as those operations necessary to upgrade or refurbish the system to fits with new project specifications or to fit with new legal requirements.
Preventive (or proactive) maintenance refers to those activities performed, according to preliminary analysis and to predefined criteria, at fixed time periods with the aim to reduce both the probability of a failure and the normal wear and tear of the system. This category includes also the ordinary maintenance, intended as those operations, foreseen by the operation and maintenance manuals, which can be executed on components and subsystems using standard tools.
Availability on site of a proper spare parts kit and execution of all services and/or replacement of parts by trained personnel help to minimize the downtime for either failures or execution of activities.
Activities of both categories could be performed by resident engineers that will assist to normal operations and perform all type of maintenance.
CMC Industries offer can include, according to customer's requirements / needs, the following different service levels:
Silver level: (costs are based on incurred costs) inclusive of spare parts service, corrective and extraordinary maintenance
Gold level: (costs are based on incurred costs plus forfeit for preventive maintenance) inclusive of services foreseen for Silver level plus preventive maintenance
Platinum level: (forfeit costs) inclusive of services foreseen for Gold level conductive maintenance. Spare resources to cover the fluctuation of site Team (day shifts / holidays / sickness periods) are foreseen in the global package
Modernization
After many years of service also CMC Industries systems and products approaches to the end of their expected operative life and, even if the robustness and high reliability are unchanged, they have to cope either with the unavoidable obsolescence of parts with the unavailability of spare parts or with new legal or technological requirements that may have changed considerably.
Operative lifetime can be extended over the initially estimated period by customized modernization activities that will bring the system / product to a new life.
Among all the advantages provided to the Customers by modernization activities, could be highlighted topics like reduction of service costs, adherence to new legal or operative requirements, increased energy efficiency with the consequent reduction of operative costs.
Modernization is not intended as a simple replacement of worn or obsolete parts with new component, it could arrive to include a complete redesign of systems and products.
CMC Industries experienced Team is ready to works closely with Customers' Team to analyze all the requirements facing the most challenging conditions and approaching the new challenges as an opportunity for further growth, and advice for everything needed to plan an optimized roadmap for implementing the agreed changes and return in operation in the shortest possible timeframe.
Upon returning in operation without surprises and with the minimum operational impact, system and products will begin their new life demonstrating to the Customer all the advantages that the modernization provides.
In case you would be interested in more details concerning our remote support / hotline service, or whether you would require on-site assistance or spare parts, you are kindly asked to contact us at indicated phone / e-mail addresses or to fill the contact form here below.
Spare parts and e-commerce (selected products only)
Spare parts service is not only referred to the supply of replacement parts rather to a complete management service that help the Customer overcoming the electromechanical wear and obsolescence of components that could lead to issues like malfunction of the equipment and for the safety of personnel.
CMC Industries assumes that all its Customers would expect to perform their business around the clock, all the days of the year, consequently the availability of genuine and high quality parts is a crucial factor to this goal.
Our Customer Service Team organizes tailor-made services for providing to all our Customer a fast delivery of correct parts however, to maximize the operating efficiency of a system, we recommend to have at least an emergency package available on site to minimize the risk level and the time to repair.
Our engineers will take over quickly and reliably the installation on site, then parts used during maintenance activities will be replaced.
This initial package of parts will be configured with all the critical / important components necessary to assure the availability of the system taking in the due consideration all expects like availability requirements, procurement and transport times and cost minimization.
CMC Industries spare parts service is available with two different alternative strategies to allow the Customers' choosing what fit better for its need:
"Standard service" foresees a local storage for all purchased parts. When a new part is needed, our Team provides, with a short reaction time, for a smooth execution of all processes that are behind the fastest possible delivery to the site of high-quality spare parts.
"Customized service" foresees a mix of critical parts stored locally by the Customer and most of the parts stored, on Customer behalf, by CMC Industries premises against a service fee. Customer may purchase parts belonging to its stock anytime through a dedicated webshop for spare parts while our Team will provide for ensuring the optimal stock level of all parts and for the almost immediate shipment through Couriers everywhere in the world.
CMC Industries Service Team is always available to assist for the identification of correct spare parts, we will just need from you few information like site location, type of machine, possibly the serial number, and a short description of the problem; with these few information our Team is able to process your request straight away.